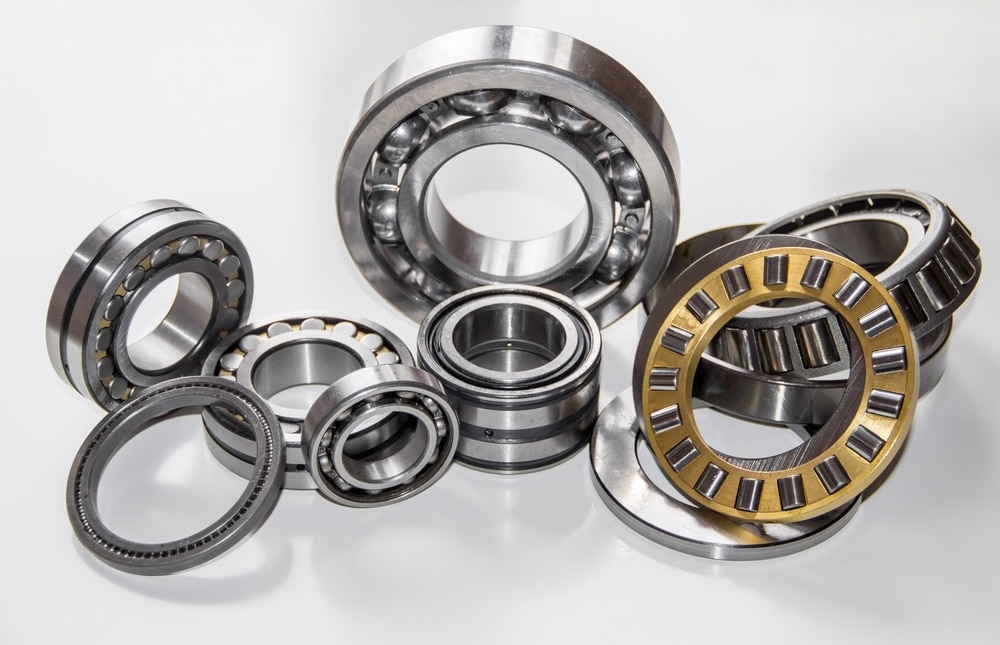
Discover the different types of bearings, including ball, roller, and sleeve bearings, and learn how to select the right bearing for your specific application to ensure optimal performance and longevity.
Discover the different types of bearings, including ball, roller, and sleeve bearings, and learn how to select the right bearing for your specific application to ensure optimal performance and longevity.
Bearings are fundamental components in mechanical systems, designed to reduce friction between moving parts, support loads, and enhance the efficiency and longevity of machinery. Essentially, a bearing facilitates the desired motion—whether it’s rotational, linear, or a combination of both—while minimizing energy loss due to friction. The basic design of a bearing consists of an inner and outer ring with a set of rolling elements, such as balls or rollers, positioned between them. This simple yet ingenious design allows machines to operate smoothly and reliably, even under varying loads and speeds.
In mechanical engineering, bearings are ubiquitous, and they are found in applications ranging from the tiny precision bearings in a wristwatch to massive industrial bearings in wind turbines. The specific bearing type can significantly impact a machine’s performance, durability, and efficiency, making it crucial to select the right bearing for each application.
Bearings are essential for the smooth operation of countless mechanical systems. By reducing friction, they prevent wear and tear on components, improve energy efficiency, and allow for the accurate and controlled movement of parts. The importance of bearings is evident in their widespread use across various industries, from automotive and aerospace to electronics and household appliances.
In automotive applications, for example, bearings are used in the wheels, transmission, and engine, where they must withstand high loads, speeds, and temperatures. In the aerospace industry, bearings are crucial for ensuring the reliable operation of critical components such as jet engines, landing gear, and control systems. In industrial machinery, bearings support heavy loads, reduce downtime, and contribute to the overall efficiency of production processes. Without bearings, many modern machines and devices would not function as smoothly or efficiently, if at all.
Rolling element bearings are perhaps the most common type of bearing used today. They feature rolling elements—either balls or rollers—between the inner and outer rings. These rolling elements minimize the contact surface area between moving parts, significantly reducing friction and wear. This category includes several types of bearings, each designed for specific applications and load conditions.
As the name suggests, ball bearings use spherical rolling elements (balls) to maintain the separation between the bearing races. This design allows for low friction, high-speed operation, and the ability to handle radial and axial loads. Ball bearings are versatile and widely used in applications requiring precision and reliability, such as electric motors, automotive components, and household appliances. Their simplicity and efficiency make them a go-to choice for many engineers and designers.
Unlike ball bearings, roller bearings use cylindrical or tapered rollers to carry the load. This design allows them to support heavier loads compared to ball bearings. Roller bearings are commonly found in industrial applications where high load capacity and durability are essential, such as in gearboxes, conveyor systems, and heavy machinery. The rollers’ shape reduces the bearing’s stress, allowing it to handle greater loads without compromising lifespan or performance.
Plain bearings, also known as bushings or sleeve bearings, do not contain rolling elements. Instead, they operate with sliding motion between the bearing surfaces, typically involving a lubricating film that reduces friction. Plain bearings are simple, reliable, and can handle heavy loads, making them ideal for applications requiring low speed and high load, such as in hinges, pivots, and sliding doors. Their design also makes them suitable for environments where maintenance and lubrication might be challenging, as they can operate effectively with minimal lubrication.
Fluid bearings use a thin layer of liquid or gas to support the load and eliminate contact between moving parts. This design provides virtually frictionless operation, which is especially beneficial in high-speed, high-precision applications. Fluid bearings are commonly used in hard drives, turbines, and other equipment where precision, quiet operation, and longevity are paramount. The absence of physical contact between the moving parts also means that fluid bearings can last longer and require less maintenance than traditional bearings.
Magnetic bearings support a load using magnetic levitation, allowing for contact-free motion. They are ideal for high-speed and high-precision applications where conventional bearings would suffer from friction and wear. Magnetic bearings are often found in advanced technologies such as MRI machines, turbochargers, and flywheel energy storage systems. They offer the advantage of operating without lubrication and can function in extreme environments, including vacuum conditions.
Jewel bearings use small, precision-made jewels as the bearing surface, offering very low friction and high durability. These bearings are typically used in sensitive instruments like watches, meters, and gyroscopes, where precision and minimal friction are crucial. The hardness of the jewel material, usually sapphire or ruby, ensures long-lasting performance, even under continuous operation.
Deep groove ball bearings are the most widely used type of ball bearing. They are versatile, capable of handling both radial and axial loads, and can operate at high speeds. These bearings are commonly used in electric motors, automotive applications, household appliances, and agricultural machinery. The deep grooves on the inner and outer rings allow the bearing to accommodate misalignment and axial loads, making them highly adaptable for various applications.
Angular contact ball bearings are designed to handle both radial and axial loads, with the ability to support high-speed operation. The contact angle in these bearings allows them to carry heavier axial loads in one direction, making them ideal for applications with combined loads. They are commonly used in machine tools, robotics, automotive steering, and aerospace components. The precision and reliability of angular contact ball bearings make them a preferred choice in applications where accuracy is critical.
Single row cylindrical roller bearings are known for their high radial load capacity, making them suitable for heavy-duty applications. These bearings are commonly used in machine tools, electric motors, gearboxes, and steel mills. The cylindrical rollers provide a larger contact area with the bearing raceways, distributing the load more evenly and reducing stress on the bearing. This design also allows for high-speed operation with minimal friction.
Double row cylindrical roller bearings provide increased load capacity and rigidity compared to their single-row counterparts. They are ideal for applications requiring higher load handling and greater stability, such as in heavy machinery, the railway industry, wind turbines, and construction equipment. The double row design helps in distributing the load evenly across the bearing, enhancing its durability and operational life.
Additionally, precision-grade double row cylindrical roller bearings can also be used in the spindles of machine tool lathes, offering high stability and accuracy in these applications.
Cross roller bearings feature cylindrical rollers arranged in a cross pattern, providing high rigidity and precision. These bearings can simultaneously handle loads from multiple directions, making them ideal for robotics, machine tools, medical equipment, and aerospace applications where precision and stability are critical. The unique design of cross-roller bearings allows them to maintain high accuracy even under varying loads and conditions.
Fluid dynamic bearings (FDB) are widely used in computers and consumer electronics, offering quiet operation and longevity due to the absence of contact between moving parts. FDBs use a fluid, typically oil, to create a dynamic pressure that supports the bearing load. This type of bearing is especially valued in applications where noise reduction and smooth operation are critical, such as in hard drives and cooling fans. The lack of physical contact between the moving parts also means that fluid dynamic bearings experience minimal wear, resulting in longer service life.
Flexible bearings are essential components in strain wave drives, which are commonly used in robotics and aerospace for precise motion control. These bearings are designed to handle the complex motion required in wave generators, allowing for compact and lightweight designs while providing high torque and precision. Flexible bearings are critical in applications where space and weight are at a premium, such as in robotic arms, aerospace control systems, and medical devices.
Selecting the right bearing for your application is crucial for ensuring optimal performance, longevity, and efficiency of your machinery. With the wide variety of bearing types available, understanding the specific needs of your application is the first step in making an informed choice. For more detailed information on different types of bearings and to explore a wide range of product options, visit our product page. Whether you’re working on a robust industrial machine or motors, you’ll find the bearings you need to ensure smooth, reliable operation.