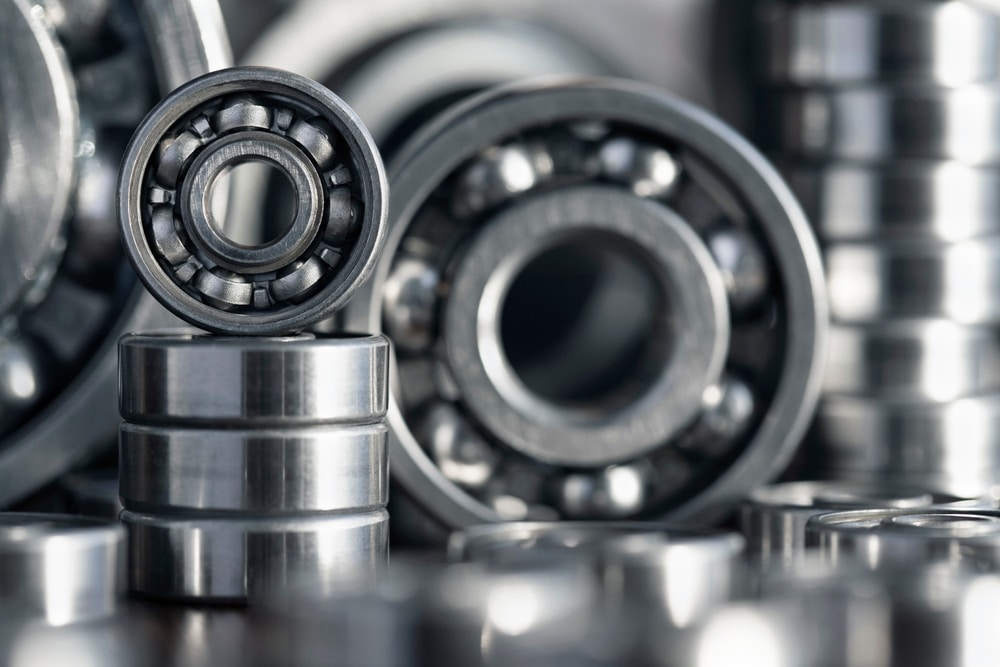
Compare sleeve bearings and ball bearings, exploring their design, performance, and typical applications to help you choose the right bearing for your needs. Discover the benefits and cost considerations of each type.
Compare sleeve bearings and ball bearings, exploring their design, performance, and typical applications to help you choose the right bearing for your needs. Discover the benefits and cost considerations of each type.
Sleeve bearings, or plain or bush bearings, are simple mechanical components that provide a bearing surface for rotating shafts. These bearings consist of a cylindrical sleeve, usually made of metal, plastic, or composite materials, that encases the rotating shaft. The inner surface of the sleeve bearing slides against the shaft, facilitating smooth movement while minimizing friction. The simplicity of the design makes sleeve bearings reliable and easy to manufacture, which contributes to their widespread use in various applications.
One of the primary advantages of sleeve bearings is their low maintenance requirements. Unlike ball bearings, sleeve bearings do not have moving parts such as balls or rollers, which reduces the need for regular lubrication and maintenance. Additionally, sleeve bearings are typically more cost-effective than ball bearings in terms of initial cost and long-term maintenance. Their simple construction and fewer components make them less expensive to produce, and their durability under low-stress conditions means they often last longer without requiring attention.
Sleeve bearings are best suited for applications where low to moderate speeds and light loads are involved. They are commonly used in fans, blowers, and electric motors, where their ability to operate quietly and efficiently under light loads is highly valued. In these environments, sleeve bearings provide a cost-effective solution that delivers adequate performance without high precision or frequent maintenance. For example, sleeve bearings are preferred in cooling fans due to their quiet operation and lower cost, making them an excellent choice for consumer electronics and home appliances.
Ball bearings are more complex than sleeve bearings, consisting of several key components: the balls, inner and outer races, and the cage (or retainer). The balls are the rolling elements that separate the inner and outer races, allowing for smooth, low-friction movement. The races are the tracks on which the balls roll, and the cage holds the balls in place, ensuring even spacing and preventing them from clumping together. This design allows ball bearings to support both radial and axial loads, providing high precision and efficiency in a wide range of applications.
Ball bearings are renowned for their precision and efficiency, making them ideal for applications requiring high performance, such as automotive, aerospace, and industrial machinery. The rolling motion of the balls reduces friction significantly compared to sliding motion in sleeve bearings, which allows ball bearings to operate at higher speeds with greater efficiency. This precision also translates into a longer lifespan and better performance under high-stress conditions, where maintaining accuracy and reducing wear are critical.
Ball bearings are used in a wide range of applications that demand reliability and precision. In the automotive industry, they are found in wheel hubs, transmissions, and engines, where they handle significant loads and high speeds. In aerospace, ball bearings are essential for the smooth operation of control systems, landing gear, and engines. Industrial machinery, such as conveyors, pumps, and gearboxes, also rely on ball bearings to sustain heavy loads while maintaining efficiency and durability.
When comparing the durability and lifespan of sleeve bearings versus ball bearings, it’s important to consider the operating conditions. Sleeve bearings typically have a longer lifespan in low-speed, low-load applications with minimal maintenance. However, ball bearings generally outperform sleeve bearings in high-speed or high-load environments due to their ability to handle greater stress without excessive wear. The rolling elements in ball bearings distribute loads more evenly, reducing the contact area and wear, which extends their operational life under demanding conditions.
Noise levels are a significant factor when choosing between sleeve and ball bearings. Sleeve bearings are known for their quiet operation, particularly at lower speeds, making them ideal for applications where noise reduction is critical, such as in HVAC systems and consumer electronics. On the other hand, ball bearings, while generally noisier, provide better performance at higher speeds and under higher loads. In high-speed applications, the noise generated by ball bearings can be mitigated with proper lubrication and advanced design features, but they are still typically louder than sleeve bearings.
Efficiency and power consumption are closely linked in the performance of bearings. Ball bearings offer higher efficiency due to their rolling motion, which reduces friction compared to the sliding motion in sleeve bearings. This increased efficiency means that ball bearings generally consume less power and generate less heat, making them more suitable for applications where energy conservation is a priority. However, in low-speed, low-load applications, the difference in efficiency may be negligible, and sleeve bearings could be preferred due to their lower cost and simpler maintenance.
When analyzing the long-term costs of sleeve versus ball bearings, several factors need to be considered, including initial purchase price, maintenance costs, and the potential need for replacement. Sleeve bearings are typically less expensive upfront and have lower maintenance requirements, making them cost-effective for applications with light loads and minimal speed. However, ball bearings’ higher precision, efficiency, and durability in more demanding applications can result in lower long-term costs despite a higher initial investment. The reduced power consumption, lower wear rates, and longer lifespan of ball bearings can offset their higher purchase price over time.
In scenarios where high performance, precision, and durability are required, ball bearings may prove to be more economical over time. For instance, in industrial machinery, where downtime is costly, ball bearings’ reliability and extended lifespan can lead to significant savings by reducing the frequency of maintenance and replacements. Additionally, in applications where energy efficiency is critical, the lower power consumption of ball bearings can result in ongoing operational cost savings, further justifying the higher upfront cost. Explore the long-term cost benefits of ball bearings.
Choosing the right bearing for your application is a critical decision that impacts your machinery’s performance, efficiency, and longevity. Whether you need the simplicity and cost-effectiveness of sleeve bearings or the precision and durability of ball bearings, selecting the right type for your specific needs is essential. For expert advice and assistance in making the best choice, our team is ready to help you find the perfect bearing solution for your application, ensuring optimal performance and value.